This is something I tend to be weak on when it comes to answering in an interview (it does not come up much). Hence this post to begin to get things ticking over in my brain.
Continuous improvement (CI) is something I’ve routinely done as I’ve updated documents, mapped business processes or followed procedures. I’ve not followed any official 6 sigma methodology (also known as Lean, Agile, Kaizen) as such, though I have the basics if this in my survival kit and ask why 5 times.
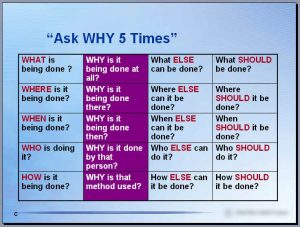
Ask Why 5 Times – pinned to the wall of my cubicle/office
CI is a method for identifying opportunities for streamlining work and reducing waste.
Where I have worked, there is no choice but to use a single contact plate to monitor a site, or a swab here and a swab there, to double glove, to filter samples with a specified volume of diluent etc. The use of IPA and sterile wipes and hand sanitiser should not be skimped on. Petri dishes need a certain volume of media. I have found the only areas in which waste can be reduced is in sundry items such as stationary and support materials. Lab inventories are controlled well enough that dehydrated media and prepared media rarely, if ever pass an expiry date, and thus does not need discarding. At best, buying cheaper materials will save on cost, but I’ve seen trying to save here can mean a reduction in quality and more time spent investigating out of specification results or investigating other issues.
The improvements to be made come from areas such as documentation, method (development and) review and computer use.
Documentation:
I’ll examine it for ways to improve both a/ the document and /b the process. This may be a result of mapping the business process, reviewing the regulations, or reviewing my own notes on what needs to be done to the document the next time it is due for update. The criticality of updates, I would have determined via a risk assessment, so the non-critical updates should be the only ones needed at routine document review time. Conducting a risk assessment allows me to determine if decisive action is required. Gain: saves time updating documents.
When printing draft documents, use a draft printer setting. Gain: saves on ink or toner.
Keep an eye on personal printing and photocopying. Gain: reduces paper consumption.
Method (Development and) Review:
If it is a new method it’ll be ideally developed to be regulatory compliant and no extra steps will be included. The process will be mapped correctly and only the required information will be in the validation documentation and final SOP’s and OI’s. Opportunities to improve methods come in the form of repeat testing that was unforeseen. By determining why such testing was required, I can set up systems to reduce the likelihood that future methods will have the same issues, and thus only the specified amount of testing. Gain: reduced need for repeat or follow-up testing.
When reviewing validated methods against the regulations, I find observing an analyst conducting the testing and asking why they do certain things is very helpful. That was I can identify what (if any) steps can be eliminated, or if there is a faster/better way of doing things. Knowing the process is on of the key pasts of the continuous improvement cycle. Gain: improved knowledge of test. Potential time savings.
The process to obtain approval signatures should not be an extensive back and forth process. I have found this to actually be fairly inefficient, no matter how hard one tries. This is why I always provide copies of any previous documents that needed changes so the signatory can see that the changes to wording, removal or addition of information has been added. That way, they should just check that the changes have been made rather the review the whole document again, which would be a waste of their time. This prevents a manager asking for information to be removed from the document and at the next request for an approval signature, asking for the same information to be provided, crazy things like that! Gain: not needing to review entire document makes for faster throughput of document approvals. Reduced duplication.
Computer Use:
I’ll check emails twice a day. If the email is not specifically for me/affects me/relates to something I am responsible for, move it to a “other” folder in case someone draws my attention to it.
If something is urgent, I’ll get (or make) a call. Gain: less time spent on emails and I only give attention to what requires it. Where issues require immediate attention, verbal or face to face communication tend to speed things up.
Given much of my work requires the use of a computer, having many tabs open with relevant information pages pinned and not using social media for personal use while at work keeps me on track. Gain: less time searching bookmarks or conducting meta searches.
I like to print PDF’s (or have the physical copy of a controlled document available) rather than view them on-screen as I can flick through them much faster than I can search for specific key words. Gain: less time hunting through documents for information.
When mentoring staff, I pass such tips along to them. Gain: team gains knowledge, improves processes.
Most importantly, when making improvements, I’ll never change things in such a way that would result in an adulterated product. An example of an often used key metric here is “reduced number of audit citations”. Gain: less work resulting from internal audits, less change of citations from third-party audits.
There’s a whole other discussion I could have on managing change which I’ll save that for another post.
Conclusion:
As a matter of course, I apply continuous improvement methodology to what I do. In all of the examples above, I do a fair bit of planning and internal processes should* have been process mapped (modeled) and incorporate a planning process.
*If not, I can do that.
Did you find this informative or useful? Please consider a small donation so I can expand and improve on what I deliver.